Kompresory to urządzenia mechaniczne, które mają na celu zwiększenie ciśnienia gazu poprzez zmniejszenie jego objętości. W praktyce oznacza to, że kompresor pobiera gaz, najczęściej powietrze, i spręża go, co prowadzi do wzrostu jego ciśnienia. Istnieje wiele różnych typów kompresorów, które różnią się zarówno zasadą działania, jak i zastosowaniem. Najpopularniejsze z nich to kompresory tłokowe oraz śrubowe. Kompresory tłokowe działają na zasadzie ruchu posuwisto-zwrotnego tłoka, który spręża gaz w cylindrze. Z kolei kompresory śrubowe wykorzystują dwa wirniki, które obracają się w przeciwnych kierunkach, co powoduje sprężenie gazu. Kompresory są szeroko stosowane w różnych branżach, od przemysłu budowlanego po medycynę, gdzie ich funkcjonalność jest nieoceniona.
Jakie są rodzaje kompresorów i ich zastosowania
Wyróżniamy kilka podstawowych rodzajów kompresorów, które różnią się zarówno konstrukcją, jak i przeznaczeniem. Kompresory tłokowe to jedne z najstarszych i najbardziej popularnych modeli, które znajdują zastosowanie w wielu dziedzinach. Są idealne do użytku domowego oraz w małych warsztatach, gdzie potrzebne jest sprężone powietrze do zasilania narzędzi pneumatycznych. Kolejnym typem są kompresory śrubowe, które charakteryzują się dużą wydajnością i są często wykorzystywane w przemyśle ciężkim oraz produkcji. W przypadku większych zakładów przemysłowych stosuje się również kompresory spiralne oraz łopatkowe, które zapewniają jeszcze wyższą efektywność pracy. Warto również wspomnieć o kompresorach bezolejowych, które są idealne do zastosowań wymagających czystego powietrza, takich jak malowanie czy prace w laboratoriach.
Jakie są kluczowe zalety korzystania z kompresorów
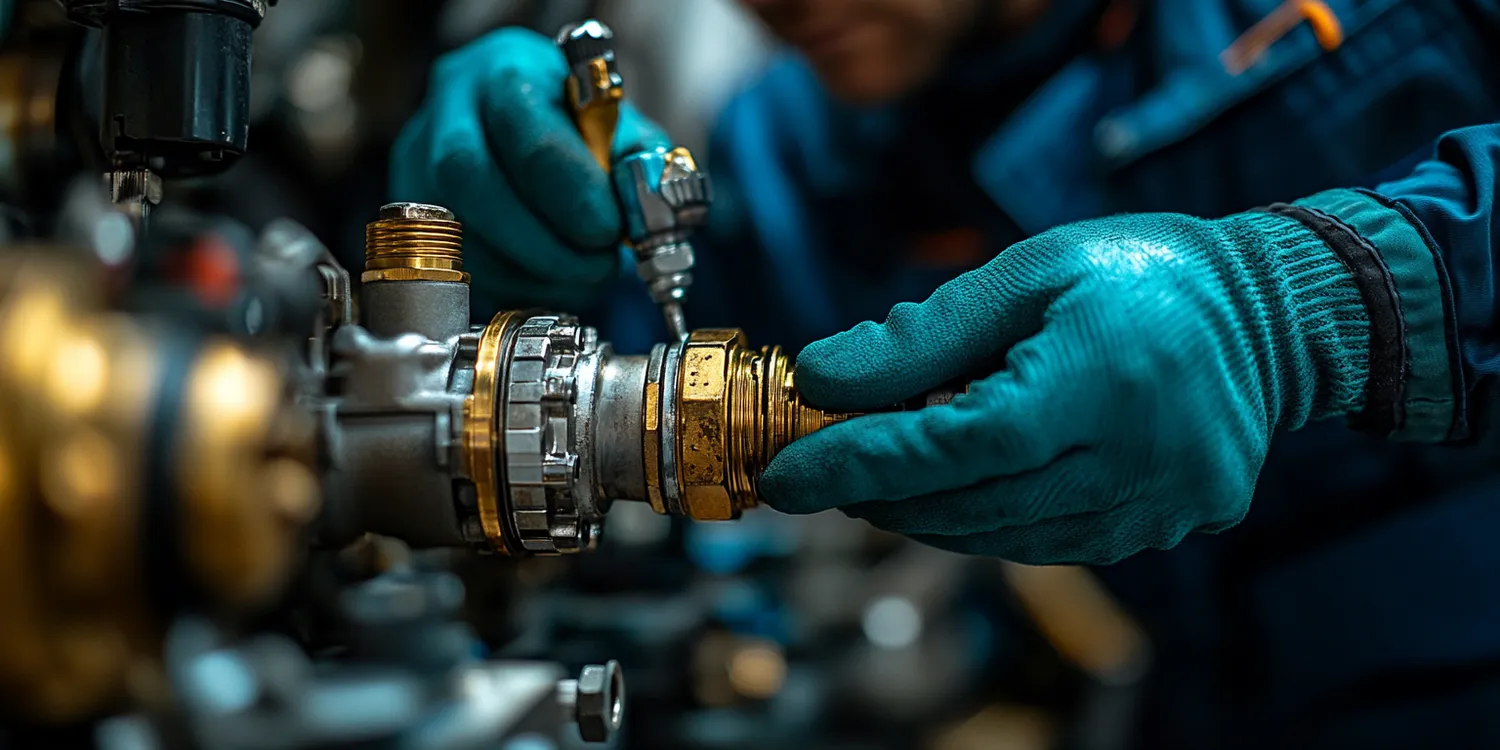
Korzystanie z kompresorów niesie ze sobą wiele korzyści, które przyczyniają się do zwiększenia efektywności pracy w różnych branżach. Przede wszystkim kompresory umożliwiają szybkie i skuteczne zasilanie narzędzi pneumatycznych, co znacznie przyspiesza procesy produkcyjne oraz remontowe. Dzięki sprężonemu powietrzu można wykonywać różnorodne zadania, takie jak malowanie, czyszczenie czy naprawa pojazdów. Ponadto kompresory pozwalają na oszczędność energii w porównaniu do innych źródeł zasilania. Sprężone powietrze może być magazynowane i wykorzystywane w momencie potrzeby, co sprawia, że nie trzeba ciągle korzystać z prądu elektrycznego. Dodatkowo nowoczesne kompresory są coraz bardziej zaawansowane technologicznie i oferują różnorodne funkcje automatyzacji oraz monitorowania pracy. Dzięki temu użytkownicy mogą mieć pełną kontrolę nad procesem sprężania powietrza oraz jego zużyciem.
Jakie są najczęstsze problemy związane z kompresorami
Mimo licznych zalet korzystania z kompresorów mogą występować pewne problemy związane z ich eksploatacją. Jednym z najczęstszych kłopotów jest niewłaściwe smarowanie elementów ruchomych, co może prowadzić do szybszego zużycia lub uszkodzenia silnika. Dlatego tak ważne jest regularne sprawdzanie poziomu oleju oraz jego jakości w przypadku kompresorów olejowych. Innym problemem może być nieszczelność układu sprężania lub przewodów powietrznych, co skutkuje utratą ciśnienia i obniżeniem efektywności pracy urządzenia. Warto także zwrócić uwagę na filtr powietrza – jego zapchanie może ograniczać przepływ powietrza i prowadzić do przegrzewania się silnika. Regularna konserwacja oraz przeglądy techniczne są kluczowe dla zapewnienia długotrwałej i bezawaryjnej pracy kompresora.
Jakie są kluczowe elementy budowy kompresora
Kompresory składają się z kilku kluczowych elementów, które współpracują ze sobą, aby zapewnić efektywne sprężanie gazu. Podstawowym komponentem jest silnik, który napędza mechanizm sprężający. W przypadku kompresorów tłokowych silnik ten zazwyczaj napędza tłok, który porusza się w cylindrze, sprężając powietrze. W kompresorach śrubowych z kolei silnik obraca wirniki, które sprężają gaz w procesie rotacyjnym. Kolejnym istotnym elementem jest zbiornik na sprężone powietrze, który gromadzi powietrze pod ciśnieniem i umożliwia jego późniejsze wykorzystanie. Zbiornik ten jest kluczowy dla stabilności ciśnienia w systemie oraz zapewnienia ciągłości pracy narzędzi pneumatycznych. Dodatkowo kompresory wyposażone są w filtry powietrza, które oczyszczają pobierane powietrze z zanieczyszczeń, a także zawory bezpieczeństwa, które chronią urządzenie przed nadmiernym ciśnieniem. Warto również wspomnieć o układzie chłodzenia, który zapobiega przegrzewaniu się kompresora podczas intensywnej pracy.
Jakie są najważniejsze czynniki przy wyborze kompresora
Wybór odpowiedniego kompresora to kluczowa decyzja, która może mieć znaczący wpływ na wydajność pracy oraz koszty eksploatacji. Przede wszystkim należy określić, do jakich celów będzie używany kompresor. Inne wymagania będą miały narzędzia pneumatyczne stosowane w warsztacie samochodowym, a inne w przemyśle budowlanym czy malarskim. Ważnym czynnikiem jest również wydajność kompresora, mierzona w litrach na minutę lub metrach sześciennych na godzinę. Warto zwrócić uwagę na maksymalne ciśnienie robocze, które powinno być dostosowane do wymagań używanych narzędzi. Kolejnym aspektem jest typ kompresora – czy ma to być model olejowy czy bezolejowy. Kompresory olejowe zazwyczaj oferują wyższą wydajność i dłuższą żywotność, ale wymagają regularnego serwisowania i wymiany oleju. Z kolei modele bezolejowe są bardziej przyjazne dla środowiska i nie wymagają dodatkowej konserwacji, co czyni je idealnymi do zastosowań wymagających czystego powietrza.
Jakie są najczęstsze zastosowania kompresorów w przemyśle
Kompresory znajdują szerokie zastosowanie w różnych branżach przemysłowych, co czyni je niezwykle wszechstronnymi urządzeniami. W przemyśle budowlanym kompresory są wykorzystywane do zasilania narzędzi pneumatycznych takich jak młoty udarowe czy wiertarki, co znacznie zwiększa efektywność prac budowlanych. W zakładach produkcyjnych sprężone powietrze jest często używane do automatyzacji procesów produkcyjnych oraz jako źródło energii do maszyn i urządzeń. Kompresory mają również zastosowanie w przemyśle spożywczym i farmaceutycznym, gdzie czyste powietrze jest niezbędne do pakowania produktów oraz utrzymania odpowiednich standardów higieny. W branży motoryzacyjnej sprężone powietrze służy nie tylko do zasilania narzędzi, ale także do napełniania opon czy testowania szczelności układów pneumatycznych. Dodatkowo w sektorze medycznym kompresory są wykorzystywane do dostarczania sprężonego powietrza do aparatów oddechowych oraz innych urządzeń medycznych.
Jak dbać o kompresor aby zapewnić jego długowieczność
Aby zapewnić długowieczność i niezawodność działania kompresora, konieczna jest regularna konserwacja oraz przestrzeganie kilku podstawowych zasad użytkowania. Przede wszystkim ważne jest regularne sprawdzanie poziomu oleju w przypadku modeli olejowych oraz jego wymiana zgodnie z zaleceniami producenta. Należy również kontrolować stan filtrów powietrza i wymieniać je w razie potrzeby, aby zapewnić odpowiednią jakość sprężanego powietrza oraz uniknąć uszkodzeń silnika. Regularne przeglądy techniczne pozwalają na wcześniejsze wykrycie ewentualnych usterek oraz ich naprawę przed wystąpieniem poważniejszych problemów. Użytkownicy powinni również dbać o odpowiednie przechowywanie kompresora – powinien on znajdować się w suchym miejscu, chronionym przed wilgocią oraz skrajnymi temperaturami. Ważne jest także unikanie przeciążania urządzenia poprzez stosowanie go zgodnie z jego przeznaczeniem oraz zaleceniami producenta dotyczącymi maksymalnego ciśnienia roboczego i wydajności.
Jakie innowacje technologiczne dotyczące kompresorów pojawiają się na rynku
Rynek kompresorów stale się rozwija i ewoluuje dzięki nowym technologiom oraz innowacjom, które mają na celu poprawę wydajności oraz efektywności energetycznej tych urządzeń. Jednym z najważniejszych trendów jest rozwój technologii bezolejowej, która pozwala na uzyskanie czystego sprężonego powietrza bez konieczności stosowania oleju smarowego. Takie rozwiązania są szczególnie cenione w branżach wymagających wysokiej jakości powietrza, takich jak przemysł spożywczy czy farmaceutyczny. Kolejną innowacją są inteligentne systemy zarządzania pracą kompresora, które umożliwiają monitorowanie jego parametrów pracy za pomocą aplikacji mobilnych lub komputerowych. Dzięki temu użytkownicy mogą na bieżąco kontrolować wydajność urządzenia oraz reagować na ewentualne problemy zanim staną się one poważne. Ponadto producenci coraz częściej inwestują w technologie zmniejszające hałas generowany przez kompresory, co jest istotne zwłaszcza w miejscach pracy wymagających cichego otoczenia.
Jakie są koszty zakupu i eksploatacji kompresora
Koszty zakupu kompresora mogą się znacznie różnić w zależności od jego typu, wydajności oraz zastosowania. Na rynku dostępne są zarówno modele budżetowe, które można nabyć za kilka setek złotych, jak i zaawansowane urządzenia przemysłowe, których ceny sięgają nawet kilkudziesięciu tysięcy złotych. Warto jednak pamiętać, że cena zakupu to tylko część całkowitych kosztów związanych z eksploatacją kompresora. Należy uwzględnić także koszty energii elektrycznej, która jest niezbędna do jego działania, a także regularne serwisowanie i konserwację. W przypadku modeli olejowych konieczne jest również uwzględnienie wydatków na olej smarowy oraz filtry powietrza. Dodatkowo warto rozważyć potencjalne oszczędności wynikające z efektywności energetycznej nowoczesnych kompresorów, które mogą znacznie obniżyć koszty eksploatacji w dłuższej perspektywie czasowej.