Destylator przemysłowy to urządzenie, które odgrywa kluczową rolę w wielu procesach produkcyjnych, zwłaszcza w przemyśle chemicznym i petrochemicznym. Jego głównym zadaniem jest separacja cieczy na podstawie różnicy w temperaturze wrzenia składników. Proces ten polega na podgrzewaniu mieszaniny cieczy, co powoduje, że składniki o niższej temperaturze wrzenia parują, a następnie skraplają się w chłodnicy, tworząc czystszy produkt. W przemyśle destylatory są wykorzystywane do produkcji alkoholu, oczyszczania wody czy też separacji różnych substancji chemicznych. W zależności od zastosowania, destylatory mogą mieć różne konstrukcje, takie jak kolumnowe czy prostokątne, a ich wydajność może być dostosowywana do specyficznych potrzeb produkcji.
Jakie są rodzaje destylatorów przemysłowych i ich zastosowania
W przemyśle istnieje wiele różnych typów destylatorów, które są stosowane w zależności od specyfiki procesu oraz wymagań dotyczących jakości produktu końcowego. Najpopularniejsze rodzaje to destylatory prostokątne, kolumnowe oraz frakcyjne. Destylatory prostokątne są najczęściej używane w małych zakładach produkcyjnych, gdzie proces jest mniej skomplikowany. Z kolei destylatory kolumnowe charakteryzują się większą wydajnością i są stosowane w dużych zakładach chemicznych oraz rafineriach. Destylatory frakcyjne natomiast pozwalają na separację wielu składników jednocześnie i są niezwykle efektywne w przypadku złożonych mieszanin. Każdy z tych typów ma swoje unikalne zastosowania i zalety, które sprawiają, że wybór odpowiedniego urządzenia jest kluczowy dla sukcesu danego procesu produkcyjnego.
Jakie są korzyści z używania destylatora przemysłowego
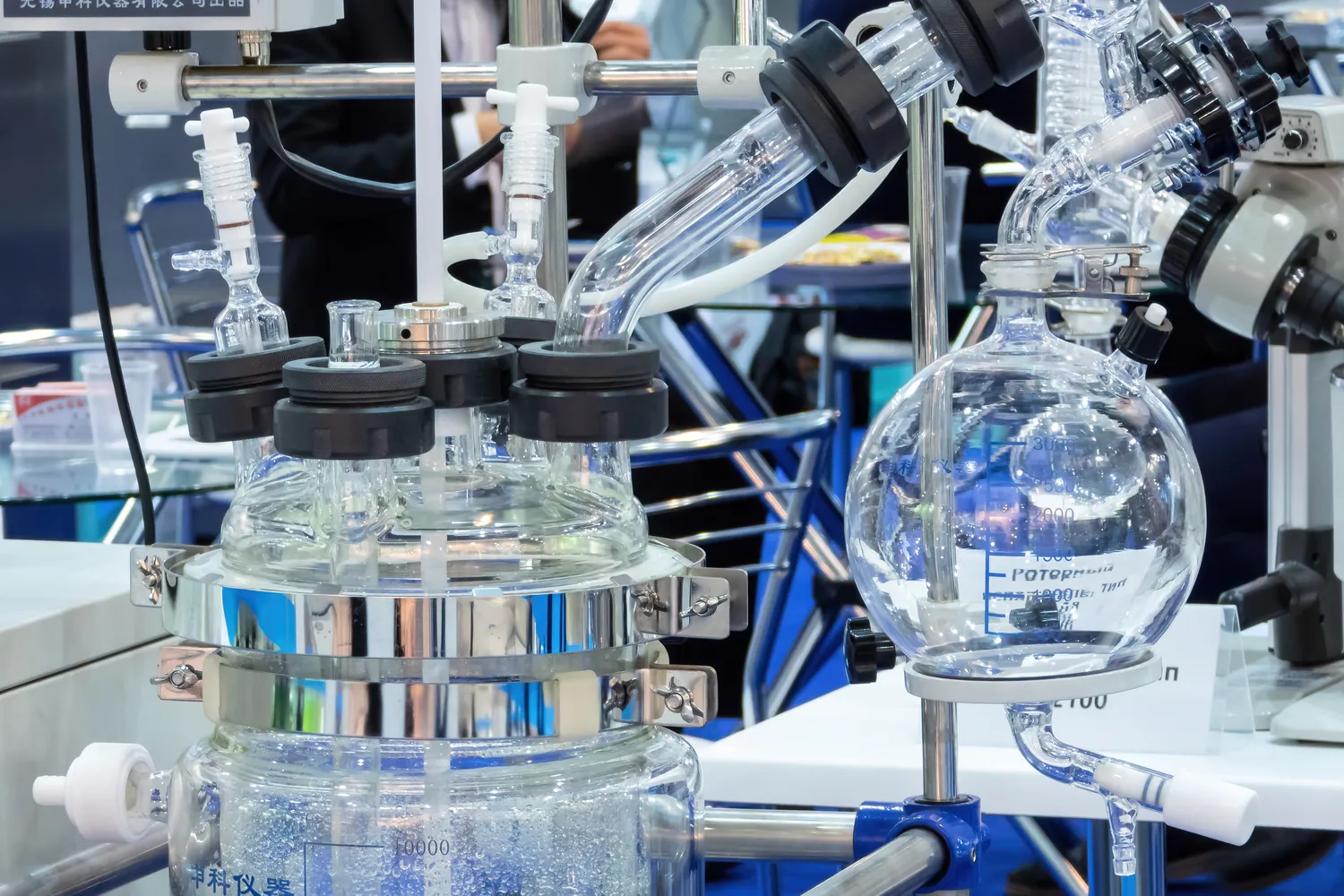
Użycie destylatora przemysłowego przynosi wiele korzyści zarówno dla producentów, jak i dla środowiska. Przede wszystkim umożliwia on uzyskanie wysokiej czystości produktów końcowych, co jest niezwykle istotne w branżach takich jak farmaceutyka czy petrochemia. Dzięki precyzyjnemu procesowi separacji można uzyskać substancje o określonych właściwościach chemicznych i fizycznych, co wpływa na jakość finalnych wyrobów. Kolejną zaletą jest możliwość recyklingu surowców – wiele procesów przemysłowych wykorzystuje destylację do odzyskiwania cennych składników z odpadów. To nie tylko zmniejsza koszty produkcji, ale także przyczynia się do ochrony środowiska poprzez ograniczenie ilości odpadów. Dodatkowo nowoczesne destylatory są coraz bardziej energooszczędne i automatyczne, co pozwala na obniżenie kosztów operacyjnych oraz zwiększenie wydajności produkcji.
Jakie są najnowsze technologie w dziedzinie destylacji przemysłowej
W ostatnich latach nastąpił znaczny postęp technologiczny w dziedzinie destylacji przemysłowej, co wpłynęło na efektywność i jakość procesów produkcyjnych. Nowoczesne destylatory często wykorzystują technologie takie jak membrany czy nanotechnologia do poprawy wydajności separacji składników. Membranowe systemy separacyjne pozwalają na eliminację potrzeby podgrzewania cieczy do wysokich temperatur, co znacząco obniża zużycie energii i koszty operacyjne. Ponadto rozwój automatyzacji i cyfryzacji procesów przemysłowych umożliwia monitorowanie i kontrolowanie pracy destylatorów w czasie rzeczywistym, co zwiększa bezpieczeństwo oraz stabilność produkcji. Technologie te pozwalają również na szybsze reagowanie na zmiany warunków procesowych oraz optymalizację pracy urządzeń.
Jakie są kluczowe czynniki wpływające na wydajność destylatora przemysłowego
Wydajność destylatora przemysłowego jest determinowana przez wiele czynników, które mogą znacząco wpłynąć na efektywność procesu separacji. Jednym z najważniejszych elementów jest temperatura, która musi być precyzyjnie kontrolowana, aby zapewnić optymalne warunki dla parowania i skraplania składników. Zbyt wysoka lub zbyt niska temperatura może prowadzić do nieefektywnej separacji i obniżenia jakości produktu końcowego. Kolejnym istotnym czynnikiem jest ciśnienie, które również ma wpływ na temperatury wrzenia poszczególnych składników. W niektórych przypadkach, takich jak destylacja próżniowa, obniżenie ciśnienia pozwala na destylację substancji w niższych temperaturach, co jest korzystne dla wrażliwych na ciepło składników. Również konstrukcja samego destylatora, w tym rodzaj zastosowanej kolumny oraz liczba teoretycznych płyt, ma kluczowe znaczenie dla efektywności procesu. Im więcej płyt, tym większa powierzchnia kontaktu między parą a cieczą, co sprzyja lepszej separacji składników.
Jakie są wyzwania związane z eksploatacją destylatorów przemysłowych
Eksploatacja destylatorów przemysłowych wiąże się z wieloma wyzwaniami, które mogą wpływać na ich wydajność oraz bezpieczeństwo pracy. Jednym z głównych problemów jest osadzanie się zanieczyszczeń i produktów ubocznych w kolumnach destylacyjnych, co może prowadzić do zmniejszenia efektywności separacji oraz konieczności częstszego czyszczenia urządzenia. Regularne konserwacje są niezbędne, aby zapewnić długotrwałą i bezawaryjną pracę destylatora. Innym wyzwaniem jest zarządzanie zużyciem energii – procesy destylacyjne często wymagają dużych ilości energii cieplnej, co może prowadzić do wysokich kosztów operacyjnych. W związku z tym wiele zakładów przemysłowych poszukuje sposobów na optymalizację zużycia energii poprzez zastosowanie technologii odzysku ciepła lub inwestycje w bardziej energooszczędne urządzenia. Dodatkowo zmieniające się przepisy dotyczące ochrony środowiska oraz normy jakościowe stawiają przed producentami nowe wymagania, które muszą być spełnione, aby uniknąć kar finansowych oraz utraty reputacji na rynku.
Jakie są zastosowania destylatorów przemysłowych w różnych branżach
Destylatory przemysłowe znajdują szerokie zastosowanie w wielu branżach, od chemicznej po spożywczą. W przemyśle chemicznym są one wykorzystywane do separacji i oczyszczania różnych substancji chemicznych, takich jak rozpuszczalniki czy kwasy. Dzięki precyzyjnej separacji można uzyskać wysokiej jakości produkty o określonych właściwościach fizykochemicznych. W branży petrochemicznej destylatory odgrywają kluczową rolę w procesie rafinacji ropy naftowej, gdzie umożliwiają uzyskanie paliw oraz innych produktów pochodnych o różnorodnych właściwościach. W przemyśle spożywczym destylatory są wykorzystywane do produkcji alkoholu oraz ekstraktów smakowych. Proces destylacji pozwala na uzyskanie czystych i intensywnych aromatów, które są niezbędne w produkcji napojów alkoholowych oraz żywności przetworzonej. Ponadto w branży farmaceutycznej destylacja jest stosowana do oczyszczania substancji czynnych oraz produkcji rozpuszczalników wykorzystywanych w lekach.
Jakie są koszty inwestycji w nowoczesny destylator przemysłowy
Koszty inwestycji w nowoczesny destylator przemysłowy mogą się znacznie różnić w zależności od wielu czynników, takich jak typ urządzenia, jego wydajność oraz dodatkowe funkcje technologiczne. Na początku należy uwzględnić koszty zakupu samego urządzenia, które mogą wynosić od kilku tysięcy do nawet milionów złotych w przypadku dużych instalacji przemysłowych. Dodatkowo należy brać pod uwagę koszty związane z instalacją oraz uruchomieniem destylatora, które mogą obejmować prace budowlane oraz elektryczne. Kolejnym istotnym elementem są koszty eksploatacyjne związane z zużyciem energii oraz materiałów eksploatacyjnych potrzebnych do pracy urządzenia. Nowoczesne destylatory często charakteryzują się wyższą efektywnością energetyczną, co może przyczynić się do obniżenia kosztów operacyjnych w dłuższej perspektywie czasowej. Ważnym aspektem jest także serwisowanie i konserwacja urządzeń – regularne przeglądy techniczne oraz ewentualne naprawy mogą generować dodatkowe wydatki.
Jakie są przyszłe kierunki rozwoju technologii destylacyjnej
Przyszłość technologii destylacyjnej zapowiada się obiecująco dzięki ciągłemu rozwojowi innowacyjnych rozwiązań oraz rosnącemu zainteresowaniu ekologicznymi metodami produkcji. W miarę jak przemysł staje przed wyzwaniami związanymi z ochroną środowiska i efektywnością energetyczną, technologia destylacji będzie ewoluować w kierunku bardziej zrównoważonych praktyk. Można spodziewać się dalszego rozwoju systemów odzysku ciepła oraz zastosowania odnawialnych źródeł energii do zasilania procesów destylacyjnych. Również automatyzacja i cyfryzacja będą miały kluczowe znaczenie dla przyszłości tej technologii – inteligentne systemy monitorowania i zarządzania procesami pozwolą na jeszcze lepszą kontrolę nad parametrami pracy urządzeń oraz szybsze reagowanie na zmiany warunków operacyjnych. Innowacje takie jak wykorzystanie nanotechnologii czy membranowych systemów separacyjnych mogą przyczynić się do poprawy wydajności procesów separacyjnych oraz redukcji kosztów operacyjnych.
Jakie są kluczowe aspekty bezpieczeństwa w pracy z destylatorami przemysłowymi
Bezpieczeństwo w pracy z destylatorami przemysłowymi jest niezwykle istotnym zagadnieniem, które wymaga szczególnej uwagi ze strony operatorów oraz zarządzających zakładami. Przede wszystkim, należy zadbać o odpowiednie szkolenie personelu, aby każdy pracownik był świadomy potencjalnych zagrożeń związanych z obsługą urządzeń. Kluczowym elementem jest również regularne przeprowadzanie inspekcji technicznych oraz konserwacji destylatorów, co pozwala na wczesne wykrywanie ewentualnych usterek i zapobieganie awariom. Warto także wdrożyć systemy monitorowania parametrów pracy urządzeń, co umożliwia szybką reakcję na nieprawidłowości. Dodatkowo, stosowanie odpowiednich środków ochrony osobistej oraz zabezpieczeń technicznych, takich jak zawory bezpieczeństwa czy systemy alarmowe, może znacząco zwiększyć poziom bezpieczeństwa w zakładzie.