Destylacja rozpuszczalników to proces, który polega na oddzieleniu substancji na podstawie różnicy w ich temperaturach wrzenia. W praktyce oznacza to, że ciecz jest podgrzewana do momentu, w którym zaczyna parować, a następnie para jest schładzana i kondensowana z powrotem do formy cieczy. Kluczowym elementem tego procesu jest zastosowanie kolumny destylacyjnej, która umożliwia wielokrotne skraplanie i parowanie substancji, co prowadzi do ich dalszego oczyszczenia. Warto zauważyć, że destylacja może być przeprowadzana w różnych warunkach ciśnienia, co wpływa na temperatury wrzenia poszczególnych składników. W przypadku destylacji prostej, stosuje się jedną kolumnę, natomiast w destylacji frakcyjnej wykorzystuje się bardziej skomplikowane układy, które pozwalają na separację wielu składników jednocześnie. Proces ten znajduje zastosowanie nie tylko w laboratoriach chemicznych, ale także w przemyśle petrochemicznym i produkcji alkoholi.
Jakie są najczęstsze zastosowania destylacji rozpuszczalników
Destylacja rozpuszczalników ma szerokie zastosowanie w różnych dziedzinach przemysłu oraz nauki. Przede wszystkim jest wykorzystywana w produkcji alkoholi, gdzie proces ten pozwala na uzyskanie napojów o wysokiej zawartości etanolu poprzez oddzielanie go od innych składników. W przemyśle chemicznym destylacja służy do oczyszczania surowców oraz produktów końcowych, co jest kluczowe dla zapewnienia ich jakości i czystości. Kolejnym istotnym zastosowaniem jest recykling rozpuszczalników organicznych, które po użyciu mogą być poddawane destylacji w celu odzyskania czystego rozpuszczalnika do ponownego użycia. W laboratoriach chemicznych destylacja jest często stosowana do separacji i analizy związków chemicznych, co pozwala na lepsze zrozumienie ich właściwości oraz reakcji. Ponadto proces ten znajduje również zastosowanie w produkcji olejków eterycznych oraz aromatów, gdzie kluczowe jest uzyskanie czystych i intensywnych zapachów.
Jakie są różnice między destylacją prostą a frakcyjną
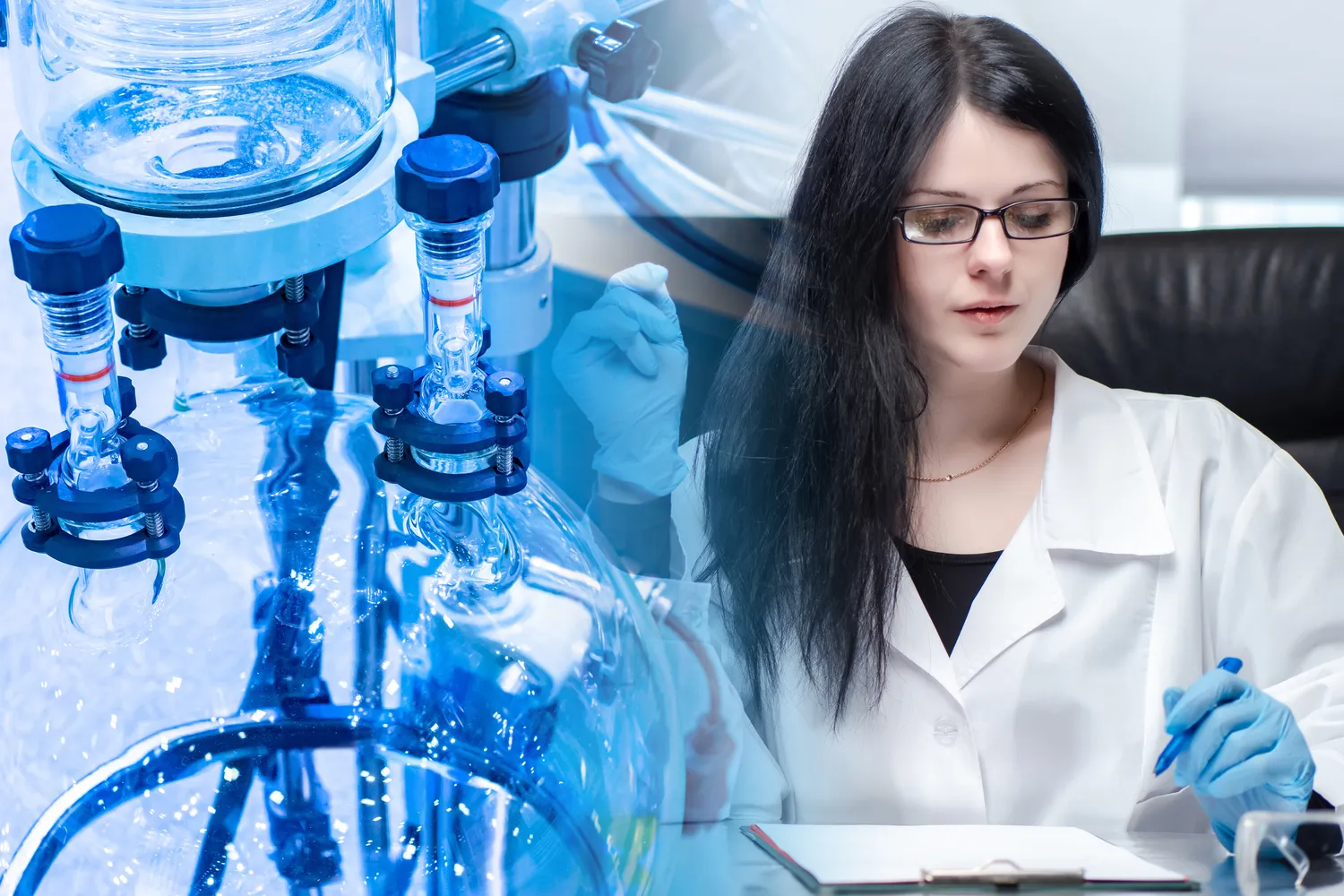
Destylacja prosta i frakcyjna to dwa podstawowe rodzaje procesów destylacyjnych, które różnią się między sobą zarówno pod względem technologicznym, jak i efektywności separacji składników. Destylacja prosta jest najprostszą formą tego procesu i polega na jednorazowym podgrzewaniu mieszaniny cieczy do momentu jej wrzenia, a następnie skraplaniu pary. Jest to metoda stosunkowo szybka i łatwa do przeprowadzenia, jednak jej skuteczność ogranicza się do sytuacji, gdy różnica temperatur wrzenia składników wynosi przynajmniej 25-30 stopni Celsjusza. Z kolei destylacja frakcyjna to bardziej zaawansowany proces, który wykorzystuje kolumny destylacyjne wyposażone w różne elementy umożliwiające wielokrotne skraplanie i parowanie. Dzięki temu możliwe jest uzyskanie wyższej czystości produktów oraz separacja składników o zbliżonych temperaturach wrzenia. Destylacja frakcyjna jest szczególnie przydatna w przypadku mieszanin złożonych, takich jak ropy naftowej czy alkohole o różnych stężeniach.
Jakie są najważniejsze czynniki wpływające na efektywność destylacji
Efektywność procesu destylacji rozpuszczalników zależy od wielu czynników, które mogą znacząco wpłynąć na jakość uzyskanych produktów oraz wydajność całego procesu. Przede wszystkim kluczową rolę odgrywa temperatura wrzenia poszczególnych składników mieszaniny; im większa różnica temperatur wrzenia, tym łatwiejsze będzie oddzielenie substancji. Kolejnym istotnym czynnikiem jest ciśnienie atmosferyczne; obniżenie ciśnienia pozwala na obniżenie temperatury wrzenia substancji, co może być korzystne w przypadku termolabilnych związków chemicznych. Również konstrukcja kolumny destylacyjnej ma znaczenie; odpowiednio zaprojektowane elementy umożliwiają lepsze skraplanie i parowanie substancji, co przekłada się na wyższą efektywność procesu. Dodatkowo czas trwania destylacji oraz szybkość podgrzewania również mają wpływ na jakość końcowego produktu; zbyt szybkie podgrzewanie może prowadzić do niepożądanych reakcji chemicznych lub degradacji substancji.
Jakie są najczęstsze błędy podczas destylacji rozpuszczalników
Podczas przeprowadzania procesu destylacji rozpuszczalników mogą wystąpić różne błędy, które negatywnie wpływają na jakość uzyskiwanych produktów oraz efektywność całego procesu. Jednym z najczęstszych błędów jest niewłaściwe ustawienie temperatury podgrzewania. Zbyt wysoka temperatura może prowadzić do niekontrolowanego parowania, co skutkuje utratą cennych składników oraz zanieczyszczeniem produktu końcowego. Z drugiej strony, zbyt niska temperatura może spowodować, że proces destylacji będzie nieefektywny, a składniki nie zostaną oddzielone w odpowiedni sposób. Innym powszechnym problemem jest niewłaściwe dobranie kolumny destylacyjnej; kolumny o zbyt małej wysokości lub niewłaściwej konstrukcji mogą ograniczać efektywność separacji, co prowadzi do uzyskania produktów o niskiej czystości. Ponadto, brak odpowiedniej kontroli ciśnienia również może wpłynąć na wyniki destylacji. Warto również zwrócić uwagę na czystość używanych materiałów; zanieczyszczone rozpuszczalniki mogą wprowadzać dodatkowe składniki do procesu, co obniża jakość końcowego produktu.
Jakie są korzyści płynące z zastosowania destylacji rozpuszczalników
Destylacja rozpuszczalników przynosi wiele korzyści zarówno w przemyśle, jak i w laboratoriach chemicznych. Przede wszystkim umożliwia uzyskanie wysokiej jakości produktów chemicznych poprzez skuteczne oddzielanie składników na podstawie ich temperatur wrzenia. Dzięki temu możliwe jest produkowanie czystych substancji, które są niezbędne w wielu procesach przemysłowych oraz badawczych. Kolejną istotną korzyścią jest możliwość recyklingu rozpuszczalników organicznych; proces destylacji pozwala na odzyskanie użytych rozpuszczalników, co przyczynia się do zmniejszenia odpadów oraz obniżenia kosztów produkcji. Dodatkowo, destylacja jest metodą stosunkowo prostą i efektywną, co sprawia, że jest szeroko stosowana w różnych dziedzinach przemysłu, takich jak petrochemia czy farmaceutyka. Proces ten pozwala także na łatwe skalowanie; można go dostosować do potrzeb zarówno małych laboratoriów, jak i dużych zakładów produkcyjnych.
Jakie są nowoczesne technologie stosowane w destylacji
W ostatnich latach rozwój technologii związanych z destylacją rozpuszczalników znacząco wpłynął na efektywność i jakość tego procesu. Nowoczesne systemy destylacyjne wykorzystują zaawansowane technologie, takie jak destylacja membranowa czy ekstrakcja cieczy z cieczą, które pozwalają na bardziej precyzyjne oddzielanie składników. Destylacja membranowa polega na wykorzystaniu specjalnych membran, które selektywnie przepuszczają określone składniki mieszaniny, co znacznie zwiększa efektywność separacji i zmniejsza zużycie energii. Innym innowacyjnym podejściem jest zastosowanie technologii mikrofalowej w procesie destylacji; mikrofalowe podgrzewanie pozwala na szybsze i bardziej równomierne podgrzewanie cieczy, co przekłada się na lepszą jakość uzyskiwanych produktów. Dodatkowo automatyzacja procesów destylacyjnych stała się standardem w nowoczesnych zakładach produkcyjnych; systemy sterowania umożliwiają precyzyjne monitorowanie parametrów procesu oraz automatyczne dostosowywanie warunków pracy urządzeń.
Jakie są różnice między destylacją a innymi metodami separacji
Destylacja to jedna z wielu metod separacji substancji chemicznych, jednak różni się od innych technik zarówno zasadą działania, jak i zastosowaniami. W przeciwieństwie do filtracji czy ekstrakcji, które opierają się na różnicy w wielkości cząsteczek lub ich rozpuszczalności w różnych rozpuszczalnikach, destylacja bazuje na różnicy temperatur wrzenia składników mieszaniny. To sprawia, że jest szczególnie skuteczna w przypadku cieczy o wyraźnie różniących się temperaturach wrzenia. Z kolei chromatografia to inna technika separacyjna, która wykorzystuje interakcje między składnikami a fazą stacjonarną; jest to metoda bardziej skomplikowana i czasochłonna niż destylacja, ale pozwala na uzyskanie bardzo wysokiej czystości produktów. Warto również zwrócić uwagę na ekstrakcję cieczy z cieczą; ta metoda polega na wykorzystaniu różnicy w rozpuszczalności składników w różnych cieczy i może być stosowana do separacji substancji o podobnych temperaturach wrzenia.
Jakie są przyszłe kierunki rozwoju technologii destylacji
Przyszłość technologii destylacji rozpuszczalników zapowiada się obiecująco dzięki ciągłemu postępowi naukowemu oraz technologicznemu. W miarę rosnącej potrzeby ochrony środowiska oraz efektywności energetycznej coraz większą uwagę przykłada się do opracowywania nowych metod separacji o niższym zużyciu energii i mniejszych emisjach gazów cieplarnianych. Jednym z kierunków rozwoju jest integracja procesów chemicznych z odnawialnymi źródłami energii; wykorzystanie energii słonecznej czy geotermalnej do podgrzewania cieczy może znacząco obniżyć koszty operacyjne oraz wpływ na środowisko. Ponadto rozwój nanotechnologii otwiera nowe możliwości w zakresie projektowania materiałów do kolumn destylacyjnych; nanostruktury mogą poprawić efektywność wymiany masy oraz ciepła w procesie separacji. Również automatyzacja procesów oraz zastosowanie sztucznej inteligencji do monitorowania i optymalizacji warunków pracy urządzeń stają się coraz bardziej popularne; te innowacje mogą przyczynić się do zwiększenia wydajności oraz jakości produktów końcowych.
Jakie są kluczowe aspekty bezpieczeństwa w destylacji rozpuszczalników
Bezpieczeństwo w procesie destylacji rozpuszczalników jest niezwykle istotne, ponieważ wiele z używanych substancji chemicznych może być łatwopalnych, toksycznych lub szkodliwych dla zdrowia. Kluczowym aspektem jest odpowiednie zabezpieczenie urządzeń oraz przestrzeni roboczej przed wyciekami i pożarami. W tym celu należy stosować materiały odporne na działanie chemikaliów oraz regularnie kontrolować stan techniczny sprzętu. Ważne jest również zapewnienie odpowiedniej wentylacji w pomieszczeniach, w których przeprowadzane są procesy destylacyjne, aby zminimalizować ryzyko gromadzenia się niebezpiecznych oparów. Pracownicy powinni być przeszkoleni w zakresie obsługi urządzeń oraz znajomości procedur awaryjnych, co pozwoli na szybką reakcję w przypadku wystąpienia zagrożeń. Dodatkowo, stosowanie odpowiednich środków ochrony osobistej, takich jak rękawice, gogle czy maski ochronne, jest niezbędne do zminimalizowania ryzyka kontaktu z niebezpiecznymi substancjami.