Budowa maszyn pneumatycznych opiera się na kilku kluczowych elementach, które współpracują ze sobą, aby zapewnić skuteczne działanie systemu. Na początku warto zwrócić uwagę na kompresor, który jest sercem każdego systemu pneumatycznego. Jego zadaniem jest sprężanie powietrza, co pozwala na uzyskanie odpowiedniego ciśnienia niezbędnego do pracy innych komponentów. Kolejnym istotnym elementem jest zbiornik powietrza, który gromadzi sprężone powietrze i utrzymuje je pod stałym ciśnieniem. Zbiorniki te są projektowane w taki sposób, aby wytrzymały wysokie ciśnienie oraz były odporne na korozję. Następnie mamy do czynienia z różnymi rodzajami zaworów, które kontrolują przepływ powietrza w systemie. Zawory te mogą być ręczne lub automatyczne, a ich odpowiedni dobór ma kluczowe znaczenie dla efektywności całego układu. Ważnym elementem są także siłowniki pneumatyczne, które przekształcają energię sprężonego powietrza w ruch mechaniczny. Siłowniki te mogą mieć różne kształty i rozmiary, w zależności od zastosowania maszyny. Ostatnim, ale nie mniej istotnym elementem są przewody pneumatyczne, które transportują sprężone powietrze do poszczególnych komponentów maszyny.
Jakie są zastosowania maszyn pneumatycznych w przemyśle
Maszyny pneumatyczne znajdują szerokie zastosowanie w różnych gałęziach przemysłu, co czyni je niezwykle wszechstronnymi narzędziami. W przemyśle produkcyjnym wykorzystuje się je do automatyzacji procesów montażowych oraz pakowania produktów. Dzięki swojej szybkości i precyzji maszyny pneumatyczne znacznie zwiększają wydajność linii produkcyjnych. W branży budowlanej stosuje się je do wykonywania prac związanych z wierceniem, cięciem czy też podnoszeniem ciężkich materiałów. Pneumatyczne narzędzia ręczne, takie jak młoty udarowe czy wkrętarki, są często wykorzystywane przez fachowców w terenie. W przemyśle motoryzacyjnym maszyny pneumatyczne są wykorzystywane do lakierowania oraz montażu elementów pojazdów, co pozwala na osiągnięcie wysokiej jakości wykonania przy jednoczesnym skróceniu czasu pracy. Również w branży spożywczej maszyny te znajdują zastosowanie przy pakowaniu oraz transportowaniu produktów, gdzie zachowanie higieny i bezpieczeństwa jest kluczowe. Warto również wspomnieć o ich roli w medycynie, gdzie stosowane są do napędu urządzeń diagnostycznych oraz chirurgicznych.
Jakie są zalety i wady maszyn pneumatycznych
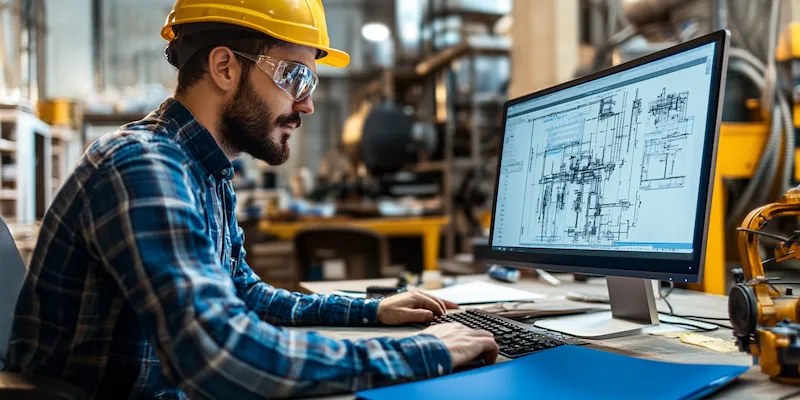
Budowa maszyn pneumatycznych wiąże się z wieloma zaletami, które przyciągają uwagę inżynierów oraz przedsiębiorców. Jedną z głównych korzyści jest ich prostota konstrukcji oraz łatwość obsługi. Dzięki temu można je szybko wdrożyć w różnych środowiskach produkcyjnych bez potrzeby skomplikowanego szkolenia personelu. Maszyny te charakteryzują się również dużą niezawodnością oraz długowiecznością, co sprawia, że inwestycja w nie jest opłacalna na dłuższą metę. Dodatkowo ich działanie opiera się na sprężonym powietrzu, co czyni je bardziej ekologicznymi niż inne źródła energii, takie jak elektryczność czy paliwa kopalne. Niemniej jednak istnieją również pewne ograniczenia związane z używaniem maszyn pneumatycznych. Przede wszystkim ich wydajność może być uzależniona od jakości sprężonego powietrza oraz ciśnienia roboczego. W przypadku niewłaściwego zarządzania systemem mogą wystąpić straty energii poprzez nieszczelności w układzie. Ponadto niektóre aplikacje wymagają większej precyzji niż ta oferowana przez maszyny pneumatyczne, co może ograniczać ich zastosowanie w bardziej skomplikowanych procesach produkcyjnych.
Jakie innowacje wpływają na rozwój maszyn pneumatycznych
W ostatnich latach obserwujemy dynamiczny rozwój technologii związanych z budową maszyn pneumatycznych, co przekłada się na ich coraz szersze zastosowanie w różnych branżach przemysłowych. Innowacje te obejmują zarówno nowe materiały konstrukcyjne, jak i zaawansowane technologie sterowania oraz automatyzacji procesów. Wprowadzenie inteligentnych systemów monitorowania pozwala na bieżące śledzenie parametrów pracy maszyn oraz szybką identyfikację potencjalnych problemów technicznych. Dzięki temu możliwe jest zminimalizowanie przestojów oraz zwiększenie efektywności produkcji. Kolejnym istotnym trendem jest rozwój siłowników pneumatycznych o zmiennej geometrii, które umożliwiają lepsze dostosowanie do specyficznych potrzeb aplikacji przemysłowych. Nowoczesne rozwiązania pozwalają także na integrację maszyn pneumatycznych z systemami robotyzacji i sztucznej inteligencji, co otwiera nowe możliwości automatyzacji procesów produkcyjnych. Warto również zwrócić uwagę na rosnącą popularność rozwiązań ekologicznych, takich jak systemy odzysku energii czy technologie minimalizujące straty sprężonego powietrza.
Jakie są najczęstsze problemy w budowie maszyn pneumatycznych
Budowa maszyn pneumatycznych, mimo wielu zalet, wiąże się także z występowaniem różnych problemów, które mogą wpływać na ich efektywność oraz niezawodność. Jednym z najczęstszych problemów jest nieszczelność układu pneumatycznego. Nieszczelności mogą występować w przewodach, złączach czy zaworach, co prowadzi do strat sprężonego powietrza i obniżenia wydajności całego systemu. W przypadku wykrycia nieszczelności konieczne jest przeprowadzenie dokładnej inspekcji oraz wymiana uszkodzonych elementów. Innym istotnym problemem jest zanieczyszczenie sprężonego powietrza, które może prowadzić do uszkodzenia komponentów maszyny. Zanieczyszczenia mogą pochodzić z otoczenia lub być wynikiem niewłaściwego działania kompresora. Dlatego tak ważne jest stosowanie filtrów oraz regularne czyszczenie układu pneumatycznego. Ponadto, niewłaściwe ustawienia ciśnienia roboczego mogą prowadzić do nieprawidłowego działania siłowników oraz zaworów, co również wpływa na ogólną wydajność maszyny. Warto również zwrócić uwagę na zużycie elementów roboczych, takich jak uszczelki czy tłoki, które z czasem mogą tracić swoje właściwości i wymagać wymiany.
Jakie są różnice między maszynami pneumatycznymi a hydraulicznymi
Maszyny pneumatyczne i hydrauliczne to dwa różne typy systemów mechanicznych, które mają swoje unikalne cechy oraz zastosowania. Główna różnica między nimi polega na medium roboczym – maszyny pneumatyczne wykorzystują sprężone powietrze, podczas gdy maszyny hydrauliczne działają na zasadzie cieczy hydraulicznej. Ta fundamentalna różnica wpływa na wiele aspektów ich działania. Maszyny pneumatyczne charakteryzują się szybką reakcją oraz prostotą konstrukcji, co sprawia, że są idealne do zastosowań wymagających dużej prędkości i precyzji. Z kolei maszyny hydrauliczne oferują większą siłę i moment obrotowy, co czyni je bardziej odpowiednimi do pracy z ciężkimi ładunkami oraz w trudnych warunkach przemysłowych. Kolejną istotną różnicą jest koszt eksploatacji – systemy pneumatyczne zazwyczaj wymagają mniejszych nakładów finansowych związanych z konserwacją i eksploatacją niż systemy hydrauliczne. Jednakże maszyny hydrauliczne często oferują lepszą kontrolę nad ruchem oraz większą stabilność w przypadku dużych obciążeń.
Jakie są trendy w projektowaniu maszyn pneumatycznych
W ostatnich latach projektowanie maszyn pneumatycznych ulega znacznym zmianom, co jest wynikiem postępu technologicznego oraz rosnących oczekiwań rynku. Jednym z głównych trendów jest dążenie do zwiększenia efektywności energetycznej systemów pneumatycznych. Producenci coraz częściej inwestują w technologie pozwalające na minimalizację strat energii poprzez zastosowanie nowoczesnych kompresorów o wysokiej sprawności oraz inteligentnych systemów zarządzania ciśnieniem. Kolejnym istotnym trendem jest rozwój automatyzacji procesów produkcyjnych, co pozwala na zwiększenie wydajności oraz redukcję kosztów pracy. Dzięki integracji maszyn pneumatycznych z systemami robotyzacji możliwe jest osiągnięcie wyższej precyzji oraz elastyczności w produkcji. W projektowaniu maszyn coraz większą rolę odgrywają także aspekty ekologiczne – producenci starają się tworzyć rozwiązania przyjazne dla środowiska, takie jak systemy odzysku energii czy technologie zmniejszające emisję hałasu. Również ergonomia pracy staje się kluczowym elementem projektowania maszyn pneumatycznych, co ma na celu poprawę komfortu użytkowników oraz zwiększenie bezpieczeństwa pracy.
Jakie są najlepsze praktyki w zakresie konserwacji maszyn pneumatycznych
Aby zapewnić długotrwałe i efektywne działanie maszyn pneumatycznych, niezwykle ważne jest przestrzeganie najlepszych praktyk w zakresie ich konserwacji. Regularna kontrola stanu technicznego wszystkich komponentów układu pneumatycznego jest kluczowa dla zapobiegania awariom i utrzymania wysokiej wydajności pracy. Warto zacząć od regularnego sprawdzania szczelności przewodów oraz złączek – nieszczelności mogą prowadzić do znacznych strat sprężonego powietrza i obniżenia efektywności całego systemu. Kolejnym krokiem powinno być monitorowanie jakości sprężonego powietrza; stosowanie filtrów oraz separatorów kondensatu pomoże w eliminacji zanieczyszczeń, które mogą uszkodzić komponenty maszyny. Należy także regularnie kontrolować ciśnienie robocze w układzie – niewłaściwe ustawienia mogą prowadzić do nieprawidłowego działania siłowników i zaworów. Dodatkowo warto pamiętać o smarowaniu ruchomych części zgodnie z zaleceniami producenta, co pozwoli na zmniejszenie tarcia i wydłużenie żywotności elementów roboczych.
Jakie są przyszłościowe kierunki rozwoju technologii pneumatycznej
Przyszłość technologii pneumatycznej zapowiada się bardzo obiecująco dzięki ciągłemu postępowi technologicznemu oraz rosnącym wymaganiom rynku przemysłowego. Jednym z kluczowych kierunków rozwoju będzie dalsza automatyzacja procesów produkcyjnych, która pozwoli na zwiększenie wydajności oraz redukcję kosztów operacyjnych. Integracja sztucznej inteligencji i uczenia maszynowego z systemami pneumatycznymi umożliwi bardziej zaawansowane zarządzanie procesami produkcyjnymi oraz optymalizację zużycia energii. Kolejnym istotnym trendem będzie rozwój rozwiązań opartych na Internet of Things (IoT), co pozwoli na bieżące monitorowanie stanu maszyn oraz przewidywanie ewentualnych awarii przed ich wystąpieniem dzięki analizie danych zbieranych przez czujniki zamontowane w urządzeniach. Również ekologia będzie odgrywać coraz większą rolę w projektowaniu nowych rozwiązań – producenci będą dążyć do tworzenia bardziej energooszczędnych systemów oraz rozwiązań minimalizujących wpływ na środowisko naturalne poprzez recykling materiałów czy stosowanie odnawialnych źródeł energii w procesach produkcyjnych.